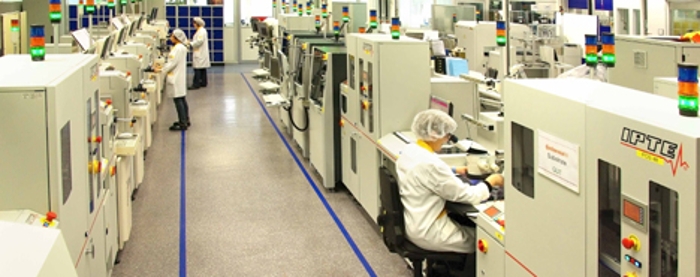
Elektronikproduktion |
IPTE verkettet Produktionsprozess bei Continental
Continental hat im Chip und Wire-Bereich die Bestückungslinie mit den Anlagen der Prozesse Bonden und AOI mit Transport- und Handlings-Modulen der IPTE Factory Automation verkettet.
Die Verkettung von einzelnen Produktionsschritten kann signifikante Vorteile bringen. Dies zeigt das Beispiel bei Continental in Nürnberg. Dort wurde im „Chip und Wire“-Bereich die Bestückungslinie mit den Anlagen der Prozesse Bonden und automatisch optische Inspektion mit Transport- und Handlings-Modulen der IPTE Factory Automation verkettet.
Continental in Nürnberg ist das weltweite Kompetenzzentrum für Hybrid-Produkte. Hergestellt werden dort beispielsweise Getriebesteuergeräte für die Automobilindustrie, die auf Schaltungsträgern aus Keramik basieren. Bestückt werden diese Keramikträger mit SMD-Bauteilen und offenen Halbleitern. Im Produktionsablauf sind mehrere Bond-Vorgänge erforderlich.
Dabei werden Gold- und Aluminiumdrähte in der Stärke von 25 bis 400 µm verwendet. Die Getriebesteuergeräte sind direkt in das Kfz-Getriebe eingebaut und dort Temperaturen von bis zu 160° Celsius ausgesetzt. Qualität und Zuverlässigkeit stehen bei diesen hohen Anforderungen natürlich an erster Stelle.
Die zusätzliche Verkettung der Produktions-Linie beginnt ab dem Prozess Goldbonden, sie verbindet noch die Prozesse Aluminiumbonden und die automatische optische Inspektion (AOI) inklusive der Verifizierung der Ergebnisse. Das Projekt wurde in enger Zusammenarbeit zwischen der Abteilung Industrial Engineering bei Continental in Nürnberg und den Automatisierungs-Spezialisten der IPTE Factory Automation realisiert.
Die Linienverkettung ermöglicht eine drastische Reduzierung der Durchlaufzeiten sowie eine Reduzierung des Warenbestandes in der Produktion. Durch eine Reduzierung der Lohnminuten pro Produkt ließ sich das Projekt auch wirtschaftlich klar darstellen.
Weitere Vorteile, die sich durch die Realisierung der Verkettung erreichen ließen waren die Reduzierung der benötigten Stellfläche um 40%, die Reduzierung des manuellen Handlings von Magazinen um 80% sowie die Reduzierung des logistischen Aufwandes durch die eindeutige Linienführung.
Mit Hilfe der Verkettung werden durch kurze Regelschleifen bis zum Verifizieren zudem Serienfehler verhindert. Darüber hinaus konnten Handlingsfehler und Pseudofehler durch eine kurze Regelschleife zwischen dem Bonden und der AOI verringert werden.
„Durch die Verkettung der Produktionsschritte spielen wir bezüglich der Qualität nun in einer ganz anderen Liga“, fasst Roland Wurm, Manager Production Engineering Chip & Wire bei Continental in Nürnberg, die Ergebnisse zusammen. „Die Anlage genießt auch bei den Mitarbeitern eine hohe Akzeptanz. Besonders hervorzuheben ist außerdem die Tatsache, dass die Investition für die Verkettung durch den Entfall von Magazinhandlern kompensiert wird. Wir haben also gleiche Maschinenkosten für die verkettete Linie bei deutlich gesteigerter Leistung und Qualität“, erklärt Wurm.
Im Einzelnen wurden sieben sowie zwei Aluminiumbonder und drei automatische optische Inspektionsanlagen verkettet. Vor und nach jedem Prozess wurde zur Erhöhung der Verfügbarkeit ein Magazinpuffer sowie eine Umfahrung einer jeden Anlage installiert. So kann bei einem eventuellen Stillstand einer Anlage oder auch aller Anlagen eines kompletten Prozesses die Produktionslinie weiter betrieben werden.
