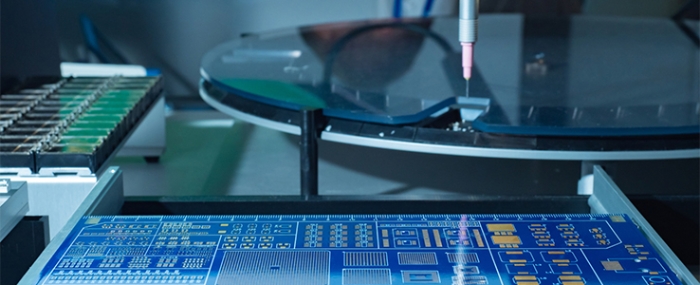
© AdobeStock
Leiterplatten |
Kann frühes DFM die Produktion Ihrer Leiterplatte beschleunigen?
Wie können Sie sicherstellen, dass Ihr PCB-Design alle erforderlichen Faktoren berücksichtigt, um die Leiterplatten herzustellen und unnötige Verzögerungen durch technische Rückfragen zu vermeiden?
Es gibt, viele Schritte bei der Leiterplattenherstellung und jedes Design muss explizit bewertet werden. Design Review Checks (DRCs) einschließlich Kupferverteilung, Stack Up Review, Registrierung, Restringe und Zeichnungsprüfung.
Die Vorbereitung der Produktionsmittel wie Filme, Bohr- und Fräsbänder sind die Basis der Produktion und wenn das Design nicht alle erforderlichen Faktoren berücksichtigt, kann dies zu vielen technischen Fragen führen, was möglicherweise zu Lieferzeitverzöerungen führt und damit die Kunden frustriert.
Was können wir also tun um das zu verhindern?
Ein guter Anfang ist DFM (Design for Manufacturing) so früh wie möglich in der Layoutphase zu nutzen. Bitten Sie uns um Ratschläge und Tips zu Themen, die als Risiko angesehen und möglicherweise verbessert werden könnten. Die Reduzierung der technischen Fragen ist für alle Beteiligten besser und die Hersteller bevorzugen es über einen sauberen Daten- / Zeichnungssatz zu verfügen, der mit minimalen Fragen direkt durch die Datenvorbereitung geht.
Überprüfen Sie, ob die Zeichnungen mit den neuesten Informationen auf dem neuesten Stand sind.
Nachfolgend haben wir einige Beispiele aufgeführt, die Sie berücksichtigen sollten.
Lagenaufbau, Materialien und Laminatdicke, Muss es sich um einen bestimmten Lagenaubau handeln?
Standardlaminatdicken variieren je nach Hersteller. Was für einen Standard sein kann, ist für einen anderen nicht auf Lager. Wenn Sie keine Isolierabstände angeben, überlassen Sie die Entscheidung dem Hersteller.
Wenn es sich um einen bestimmten Materialtyp handeln muss, ist es ebenfalls einfacher, IPC konforme Angaben zu machen, z.B. IPC 4101/99/126 auf die Materialoption, so dass der Hersteller frei wählen kann.
Wenn es sich um einen spezifischen Aufbau handelt, versuchen Sie, die Laminatdicke gleich / ähnlich zu halten. Unterschiedlich dicke Laminate bewegen sich auch unterschiedlich, während des Verpressens. Wenn alle Laminate die gleiche Dicke haben, ist dies für die Produzenten einfacher zu handhaben und Prozesse können optimiert werden.
Ist der Lagenaufbau symmetrisch , um mögliche Probleme mit Verwindung und Verwölbung zu verhindern?
Stellen Sie sicher, dass die angegebenen Prepreg-Dicken für die Endkupferstärke geeignet sind, d.h. Kupferstärken von mehr als 35um benötigen normalerweise mehr Prepreg, um eine Delaminierung zu vermeiden.
Achten Sie auf eine gleichmässige Kupferverteilung und vermeiden Sie große kupferfreie Bereiche um beim Verpressen Niederdruckbereiche zu vermeiden. Eine gleichmässige Kupferverteilung vermindert das Risiko von Faltenbildung oder Delaminierung. Hersteller werden fragen, ob sie Kupfer hinzufügen können, wenn das Risiko eines geringen Kupfergehalts besteht.
Impedanzkontrolle - haben Sie die Kontrolle darüber?
Benötigen Sie Testergebnisse, nutzen Sie Testcoupons aus dem Fertigungsnutzenrand. Wenn Sie einen definierten Lagenaufbau haben, können Sie auch eine impedanzkontrollierte Produktion ohne Test akzeptieren? Dann vermerken Sie das bitte in Ihrer Zeichnung. Vermerken Sie zudem, dass der Produzent Leiterbahnbreiten -und abstände korrigieren darf um die geforderten Impedanzen zu erreichen.
Restringe
Das Design muss mit den Zeichnungsanforderungen übereinstimmen. Wenn Sie IPC 6012 Klasse 2 oder 3 angeben, dann muss die Bohrer / Pad-Kombination für die Freigabekriterien geeignet sein.
Unter der Annahme, dass der Hersteller eine Registrierungstoleranz von 100um hat, muss diese dann zu den Restringanforderungen hinzugerechnet werden, z.B. 25um Klasse 2, 50um Klasse 3. Hier ist ein Beispiel basierend auf einer Bohrgröße von 300um;
Klasse 2 - Bohren Sie 300um, die Padgröße sollte 550um (125 + 125um) betragen.
Klasse 3 - Bohren Sie 300um, die Padgröße sollte 600um (150 + 150um) betragen.
Idealerweise nehmen die Padgrößen pro Pressvorgang zu, da die Registrierung von mehr Lagen schwieriger wird. In Fällen, in denen der Platz auf Schaltungen begrenzt ist, ist es oft nicht möglich, eine solche Kombination Bohrer / Pad zu verwenden. Dies veranlasst die Produzenten zu optimierten Pressvorgängen und der Verwendung kleinere Bohrdurchmesser.
Das Hinzufügen von Teardrops zu den Pads wird ebenfalls empfohlen, da dies dazu beiträgt, die Restringanforderungen zu erfüllen. Es sollte auch ein sicherer Abstand zwischen den gebohrten Löchern und der nächsten Kupferfläche gegeben sein, so dass keine Gefahr besteht, dass die Bohrer auf Bereiche treffen, die sie nicht treffen sollen. Typischerweise empfehlen wir einen Abstand von 178 bis 200um zwischen dem Rand des Bohrlochs und der nächstliegenden Kupferfläche.
Leiterbahnabstände und Leiterbahnbreiten
Stellen Sie sicher, dass die Konstruktionsmaße für die angegebenen Kupferdicken geeignet sind. Es ist schwierig bis unmöglich dicke Kupferschichten in der Kombination mit schmalen Leiterbahnen oder Abständen zu ätzen. Diese kann zu Kurzschlüssen führen.
Die Anzahl der Galvanikprozesse muss ebenfalls berücksichtigt werden, z.B. durchkontaktierte Bohrungen, Via in Pads, Microvias können erhebliche Anforderungen an die Beschichtung bedeuten. Die verschiedenen Galvanoprozesse haben auch Einfluss auf die Leiterbahnabstände- und breiten. Zusammen haben sie einen starken Einfluss auf Preis und Lieferzeit.
Kupfer bis zur Platinenkante führt nach dem Fräsen zu freiliegendem Kupfer. Wenn eine Kantenbeschichtung nicht zwingend erforderlich ist, dann sollte das Kupfer von der Platinenkante zurückgezogen sein. Hier sollte man den Angaben des Herstellers folgen.
Lötstopplackfreistellungen
Eine häufig gestellte Frage ist – speziell bei engen Abständen zwischen SMD Pads – welche Lötstopplackstege realisiert werden können.
Bei grünem Lötstopplack ist es das Ziel 50um Freistellung anzustreben um zwischen den Pads 75um Lötstopplackstege zu erreichen. Der Mindestabstand zwischen Pads ist idealerweise 178um, um Freistellung und Stege zu ermöglichen. Hersteller haben unterschiedliche Möglichkeiten, aber in der Regel sollte dieser Abstand für grünen Löststopplack ausreichend sein.
Andere Farben sind verfügbar, allerdings können sich die Designregeln ändern / erhöhen. Andere Farben wie grün werden oft/meistens im Siebdruckverfahren vollflächig aufgebracht. Dies führt zu differenzierten Freisparungen und Lötstopplackstegen.
Beschriftungsdruck/Legendprint
Bestückungsdruck der über die Pads geht, muss versetzt oder angeschnitten werden. Um Fragen dazu zu vermeiden reicht ein Text auf der Zeichnung dass dies erlaubt wird.
Neben diesen Vorschlägen für die Datenstruktur ist es wichtig, dass die Zeichnungsnotizen up-to-date mit den neuesten Standards und Anforderungen sind. Jede Abweichung, die von der Zeichnung zulässig ist, sollte hervorgehoben werden, um zusätzliche technische Fragen zu vermeiden.
Wenn Sie sich über Ihr PCB-Design nicht sicher sind oder vor Herausforderungen stehen, können Sie sich gerne an uns wenden. Wir wissen aus Erfahrung, dass eine frühzeitige Einbeziehung in den Produktentwicklungsprozess und das Design unnötige Probleme und Kosten vermeiden kann.
Autor: Craig Haywood, Senior Technical Advisor bei © Elmatica / Übersetzung: Jochen Summ
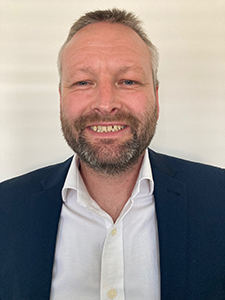
Autor: Craig Haywood, Senior Technical Advisor bei © Elmatica / Übersetzung: Jochen Summ