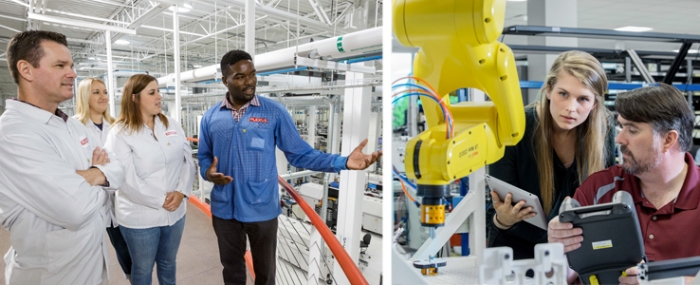
© Plexus
Elektronikproduktion |
b]Autor:[/b] Jürgen Seibert, Vice President, Business Development - EMEA at Plexus.
Eine Supply Chain ohne Verschwendung
Das Einführen von Lean Six Sigma in der Fertigung braucht mehr als nur Tools und Techniken. Entscheidend ist es, Geschäftsbereiche mit dem größten Optimierungspotential auszuwählen und Mitarbeiter unternehmensübergreifend einzubeziehen.
INur dann lassen sich die Managementmethoden als wirksames Mittel für wachsenden Kundenanforderungen, steigenden Kosten- und Leistungsdruck und schärferen Wettbewerb einsetzen. Die Mehrzahl der globalen Elektronikunternehmen steht heute unter einem enormen Druck, die Fertigungskosten zu senken, die Time-to-Market zu verkürzen und gleichzeitig mit dem rasenden Tempo an neuen Innovationen mitzuhalten. Kurze Durchlaufzeiten sind erfolgsentscheidend, so dass Managementteams alles daran setzen, die Zeit für die Markteinführung auf ein Minimum zu reduzieren. Das Management dieser Prozesse hat entscheidenden Einfluss darauf, wie effizient die Entwicklung und Markteinführung der Produkte ist. Eine wichtige Rolle spielt dabei die Supply Chain. Verschwendungen und Abweichungen treten in fast jeder Phase der Fertigung auf. Sie wirken sich negative auf die Leistungsfähigkeit aus, saugen Ressourcen ab und beeinträchtigen die Kundenzufriedenheit. In Zeiten von Nachhaltigkeit und Umweltschutz stellen sie zudem eine Gefährdung für Gesundheit und Sicherheit dar. Lean Six Sigma als Chance nutzen Die Anwendung von Lean Six Sigma sollte hier sowie in allen anderen Unternehmensbereichen eine kontinuierliche Verbesserung erreichen. Die Prinzipien lassen sich auf das in den 1940er Jahren entwickelte Produktionssystem von Toyota (TPS) zurückführen, dass bis heute als Benchmark für hocheffiziente Produktion und hohe Qualität angesehen wird. Hier bezieht sich Lean auf eine schlanke Supply Chain, in der die für den Kunden wichtigste Wertschöpfung identifiziert („Wofür ist der Kunde bereit zu zahlen?“) und Verschwendungen eliminiert wird („Wofür will der Kunde nicht zahlen?“). Six Sigma wiederum stellt einen strukturierten Ansatz dar, um Prozessvariationen zu minimieren und damit eine Fehlerfreiheit der gefertigten Produkte zu gewährleisten. Nach dem Erfolg von Toyota versuchten Hersteller immer wieder mit großem Aufwand diese Prinzipien auf ihre eigenen Fertigungsprozesse zu übertragen. Das Ziel, dass mit erheblichen finanziellen Aufwand einherging, war es, Lean Six Sigma über die gesamten Produktlebenszyklus zu implementieren, die Fertigung effizienter zu gestalten und Betriebskosten zu reduzieren. Dabei zeigte sich, dass Lean Six Sigma in der Fertigung die hohen Erwartungen nur teilweise erfüllen konnte – zumindest im Vergleich zu anderen Bereichen wie der Supply Chain. Priorität #1: Nullfehler In der Elektronikfertigung sind die Kernbereiche für eine Optimierung sehr unterschiedlich und abhängig von der Dynamik des Geschäfts. Zum Beispiel stellt die Verkürzung der Durchlaufzeit eines Produkts um eine Sekunde in einer Großserienfertigung mit geringem Mix einen bedeutenden Vorteil dar. Umgekehrt bringt der gleiche Ansatz in einer Produktion mit kleinen Stückzahlen und hohem Mix nur einen minimalen Vorteil. Dort wird der Fokus daher mehr auf die Optimierung von Anlagenumrüstungen gelegt. In einer ausgereiften Lean Six Sigma Produktion steht das Erreichen der Nullfehler-Qualität im Mittelpunkt. Das Ziel ist die Herstellung von Produkten mit Prozessen, die so gestaltet sind, dass sie auf optimaler Fähigkeitsstufe arbeiten und wenige – wenn möglich keine – Schwankungen aufweisen. Das ist besonders in stark regulierten Branchen wie der Luft- und Raumfahrt oder der Medizintechnik von enormer Bedeutung, also dort, wo bereits kleinste Abweichungen von der Norm katastrophale Folgen nach sich ziehen können. Die Messlatte für sicherheitskritische Anwendungen liegt nach wie vor hoch. Gleichzeitig wird jedoch auch hier die Zeit von der Konzeption bis zur Fertigung der Produkte immer kürzer und der Anteil an Software und Elektronik steigt. Voraussetzung für eine qualitativ hochwertige und zuverlässige Entwicklung und Fertigung ist daher die Kontrolle jeder Stufe im Entwicklungs- und Fertigungsprozess eines Produkts. Auswirkungen auf die gesamte Supply Chain Die Ausrichtung auf fehlerfreie Produkte mittels Lean Six Sigma wirkt sich direkt auf die Qualität innerhalb der Supply Chain und deren Steuerung aus. Auch Anbieter von Anlagen werden dazu verpflichtet, Prozesse zu entwickeln und Komponenten zu liefern, die dem hohen Qualitätsniveau entsprechen. Elektronikhersteller, die eine Wareneingangskontrolle und Endabnahme durchführen, sollten ihre gesamte Strategie hinsichtlich der Lieferantenentwicklung aus der Lean Six Sigma Perspektive überprüfen, um den Kunden vor fehlerhafter Ware zu schützen. Damit richtet sich der Blick zurück auf die Optimierung von Lieferantendienstleistungen und die Qualität der zugekauften Komponenten. Wenn diese Taktik effektiv eingesetzt wird, dann ergibt sich als Folge eine deutliche Reduzierung der Notwendigkeit für Inspektionen und Prüfungen. Die Übertragung von Lean Six Sigma auf die Supply Chain kann unternehmensübergreifend entscheidende Vorteile sowie deutliche Verbesserung in der Lieferperformance mit sich bringen. So lässt sich beispielsweise der Warenbestand reduzieren und Lagerkapazitäten einsparen. Das Reduzieren von gebundenem Betriebskapital wiederum verbessert den Cash Flow und erhöht langfristig die operativen Margen. Das Team einbeziehen Ob Fertigung oder Supply Chain – die Umsetzung von Lean Six Sigma setzt mehr als nur das Nachahmen von bekannten Prinzipien voraus. Ein kritischer Erfolgsfaktor wir häufig übersehen: Der psychologische Einfluss, den die Implementierung neuer Arbeitsmethoden auf die Mitarbeiter im Unternehmen nimmt. Hier gilt es Führungskräfte zu überzeugen und frühzeitig den Support des Managements sicherzustellen. Wie erfolgreich eine Lean Six Sigma Philosophie tatsächlich in der Praxis umgesetzt werden kann, hängt davon ab, wie diese Änderungen eingeführt und gehandhabt werden. Diese Einführung kann sich stark unterscheiden, je nach Unternehmenskultur und Führungsstil, der nationalen oder lokalen Kultur, der Unternehmensgröße und Demographie, den bestehenden Geschäftspraktiken sowie der Art der Produkte und Dienstleistungen. Echte Nachhaltigkeit setzt das Engagement aller Mitarbeiter auf allen Stufen eines Unternehmens voraus, unabhängig davon ob diese bereits in Kaizen-Aktivitäten involviert sind. Zufriedenheit am Arbeitsplatz, Vielfalt und Relevanz, das Verstehen der Vision und Strategie des Unternehmens, die persönliche Entwicklung, Vergütung und Anerkennung entscheiden hier mit. Es gilt, zuzuhören und Mitarbeiter mit ins Boot zu holen. Für die nötige Sensibilisierung und Kompetenz lassen sich speziell ausgerichtete Schulungen für das Management durchführen. Vor allem braucht die Umsetzung Zeit, Durchhaltevermögen und ein hohes Maß an Motivation. Richtig umgesetzt bietet Lean Six Sigma der Elektronikindustrie jedoch umfassendes – und oft noch ungenutztes – Optimierungspotential. Toyota arbeitet nach mehr als 70 Jahren Lean Management noch immer an der kontinuierlichen Verbesserung seiner Fertigungsprozesse und sieht noch einen langen Weg vor sich, bis Verschwendungen gänzlich beseitigt sind.Jürgen Seibert © Plexus
b]Autor:[/b] Jürgen Seibert, Vice President, Business Development - EMEA at Plexus.