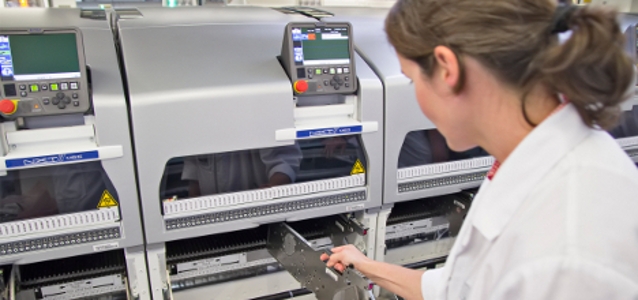
© Ihlemann
Elektronikproduktion |
Ihlemann macht SMD-Fertigung flexibler und wirtschaftlicher
Kleinere Bauteile, untypische Bauteilgeometrien, eine steigende Zahl unterschiedlicher Bauelemente auf einer Baugruppe und immer kleinere Lose sind aktuelle Trends in der Elektronikfertigung.
Der EMS-Dienstleister Ihlemann modernisiert deshalb seine SMD-Linie und setzt auf eine flexiblere Organisation der Fertigung.
EMS-Anbieter wie Ihlemann sind als Dienstleister für die Elektronikfertigung mit High-Mix-, High- und Low-Volume-Fertigungen schon immer flexibler aufgestellt als normale OEMs. Die aktuellen Trends fordern allerdings noch mehr: Es wird immer kurzfristiger bestellt, das Bestellverhalten ist sehr sprunghaft und es fehlen längerfristige Prognosen, um die Kapazitäten zuverlässig planen zu können, berichtete der ZVEI-Fachverband PCB and Electronic Systems im Sommer 2013.
„Weil ständige Produktionsänderungen und eine unsichere Zukunft inzwischen zum Normalzustand geworden sind, haben wir unsere Produktionsweise komplett umgestellt. Wir haben die Fertigung nach dem Fluss-Prinzip neu organisiert, setzen auf tägliche Verbesserungsroutinen und regelmäßiges Coaching. Dies wird ergänzt durch leistungsfähigere und flexiblere Produktionstechnologien“, erläutert Bernd Richter, Vorstand der Ihlemann AG, das neue Fertigungskonzept.
Kleinere Lose werden wirtschaftlicher
Mit der Umstellung der Produktionsorganisation sollte auch die SMD-Fertigung flexibler gemacht werden. Das Umrüsten der Linie sollte verkürzt, die Stillstandszeiten verringert und damit vor allem kleine Lose wirtschaftlicher werden. Die SMD-Linie von Fuji wurde deshalb modernisiert und mit neuen Modulen die Rüstkapazität erweitert.
Das Umrüsten auf ein neues Fertigungslos besteht vor allem aus dem Bereitstellen der benötigten Bauteile und der Eingabe der Bestückungsdaten. Einen großen Teil der Umrüstzeit benötigt der Austausch der Bauteilversorgungsstation (Feeder) mit den SMD-Bauelementen für den nächsten Auftrag. Das musste bisher vor Beginn der Bestückung erfolgen. Die höhere Rüstkapazität der neuen Module erlaubt jetzt eine Umrüstung für den nächsten Auftrag bereits noch während der Fertigung des alten Loses. Die Stillstandszeit zwischen den Aufträgen konnte so von 30 auf 15 Minuten halbiert werden.
Flexibler und wirtschaftlicher
Ein Zusatznutzen der neuen Fertigungsmodule ist die von 42.000 auf 96.000 Bauelemente pro Stunde gestiegene Verarbeitungsgeschwindigkeit. Die höhere Rüstkapazität der neuen Module ist auch auf die steigende Anzahl unterschiedlicher Bauelemente ausgerichtet. Mussten bisher 100 bis 120 verschiedene Bauteile je Baugruppe bewältigt werden, sind jetzt 200 und mehr an der Tagesordnung.
Dabei müssen die Bestückungsköpfe mit sehr kleinen Bauteilen wie 01005 oder auch sehr großen Elementen wie Stecker, Trafo´s, BGA beispielsweise für die Leistungselektronik umgehen können. Mit der kontinuierlich zunehmenden Miniaturisierung steigt auch die Anforderung an die Bestückungsgenauigkeit. Die Präzision hat sich von 50 auf 38 µm erhöht. Die höhere Flexibilität ist schließlich auch bei der Verarbeitung untypischer Bauteilgeometrien oder bei LEDs gefragt.
Eingebunden in Qualitätssicherung
Um bereits frühzeitig vor der Bestückung Lötpastendruckfehler auf Leiterplatten zu erkennen, werden diese komplett durch die Solder Paste Inspection (SPI) überprüft. Mithilfe dieses optischen 3D-Systems wird der Pastendruck auf der Leiterplatte vermessen, d.h., neben der Position können jetzt auch die Form eines Pads, die Höhe und das Volumen exakt vermessen werden.
Für die vollständige Prüfung der bestückten Leiterplatten kommt eine weitergehende AOI-Technik zum Einsatz. Mit orthogonalen und geneigten Kamerasystemen werden alle sichtbaren Lötstellen umfassend kontrolliert. Bei BGAs (Ball Grid Array) und QFNs (Quad Flat No Leads Package) mit verdeckten Anschlüssen an der Bauteilunterseite können die Lötstellen mittels Röntgentechnik überprüft werden. Es folgen elektrische Funktionstests der bestückten Leiterplatten, um die Funktionsfähigkeit der fertigen Boards sicherzustellen.