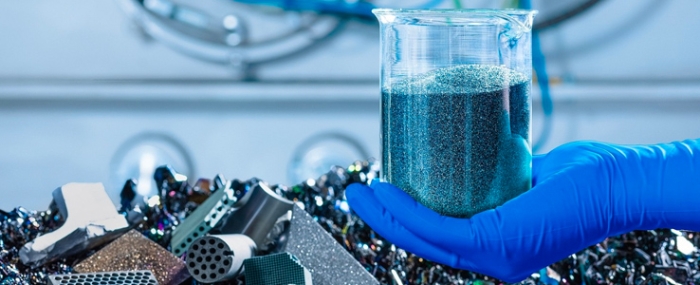
Emissionsarmes Siliciumcarbid-Recycling mit RECOSiC
Das Industriematerial Siliciumcarbid ist für viele Anwendungen begehrt, beispielsweise bei Halbleitern. Doch die Herstellung ist energieintensiv und emittiert viel Kohlendioxid. Forschende des Fraunhofer-Instituts für Keramische Technologien und Systeme IKTS haben mit RECOSiC ein besonders umweltfreundliches Recycling-Verfahren entwickelt, das diese Neben- und Abfallprodukte wieder in hochwertiges Siliciumcarbid verwandelt.
Das neuartige Verfahren verbessere die Ausbeute und reduziere auch die Abhängigkeit von Rohstofflieferanten, heißt es dazu in einer Pressemitteilung. SiC kommt bei Anwendungen in der chemischen Industrie, als technische Keramik, bei feuerfesten Komponenten, aber auch bei Halbleitern zum Einsatz. Bei der Herstellung im sogenannten Acheson-Verfahren werden Quarzsand und Petrolkoks in einem zylinderförmigen Freiluftofen auf etwa 2.500 °C erhitzt. Durch die einsetzende karbothermische Reduktion entsteht Siliciumcarbid als Endprodukt. Das Verfahren ist zwar nicht kompliziert, es entsteht jedoch sehr viel CO2. Allein durch die karbothermische Reduktion werden für 1 Tonne SiC etwa 2,4 Tonnen des klimaschädlichen Gases freigesetzt. Hinzu kommt der enorme Stromverbrauch von 7,15 MWh/t für den tagelangen Betrieb des Ofens. Hierbei entstehen weitere 1,8 Tonnen CO2 pro Tonne SiC.
„Das Acheson-Verfahren ist fast 130 Jahre alt und gehört zu den klassischen schmutzigen Industrieprozessen, die eigentlich nicht mehr in unsere Zeit passen“, sagt Jörg Adler, Abteilungsleiter Nichtoxidkeramik beim Fraunhofer-Institut für Keramische Technologien und Systeme IKTS in Dresden.
Sein Team hat nun gemeinsam mit dem Industriepartner ESK-SiC GmbH ein Recycling-Verfahren für die beim Prozess anfallenden Abfall- und Nebenstoffe entwickelt. RECOSiC reduziere die Umweltbelastung und verwandelt die recycelten Materialien in hochwertiges Siliciumcarbid. Die ESK-SiC GmbH mit Sitz in Frechen bei Köln verfügt über langjährige Erfahrung bei der Behandlung und Veredelung von Rohstoffen.
In den Randbereichen der riesigen Freiluft-Acheson-Öfen kann ein erheblicher Teil der Primär-Rohstoffe Quarzsand und Kohle nicht vollständig zu Siliciumcarbid reagieren, weil die Temperatur hier nicht hoch genug ist. Wegen der schieren Größe der Öfen und der enormen Hitze ist eine Aufstellung in der Fabrikhalle kaum möglich. Im Freiluftofen kommen Verunreinigungen aus der Luft hinzu.
Das unvollständig verwandelte SiC sowie Neben- und Abfallprodukte sind bislang nur für minderwertige Anwendungen nutzbar oder müssen entsorgt werden. Hier schaffe das patentierte RECOSiC Abhilfe.
„Wir erhitzen diese Nebenprodukte unter Schutzgasatmosphäre in einem Hightech-Ofen auf Temperaturen bis zu 2.400 °C. Daraus entsteht wieder hochwertiges SiC. Die Energieaufnahme ist bei RECOSiC um 80 Prozent niedriger als im Acheson-Prozess, damit sinkt auch der CO2-Ausstoß deutlich, so Jörg Adler.
Im Gegensatz zum Acheson-Verfahren fallen im Hightech-Ofen sehr wenig Abfälle oder Nebenprodukte an. Verunreinigungen werden im Zuge der chemischen Reaktion abgeschieden oder verdampft. Metalle wie Eisen bilden unter großer Hitze Klümpchen, die sich mechanisch entfernen lassen. Die Ausbeute liege damit bei nahezu 100 Prozent. Bei RECOSiC entstehe hochwertiges SiC mit einem Reinheitsgrad von 99 Prozent und sogar mehr, heißt es weiter.