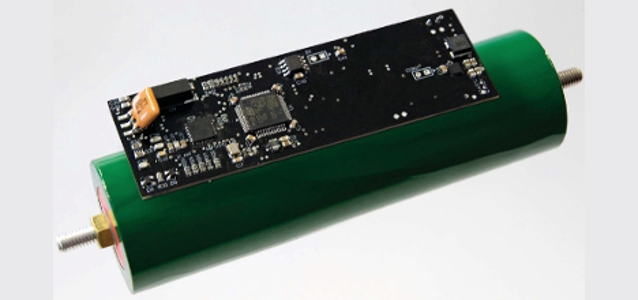
© Fraunhofer IPA
Markt |
Elektroautos: Batterie mit Köpfchen
Das Herzstück von Elektroautos sind ihre Batterien. Bislang sind diese ein monolithischer Block, in dem die einzelnen Batteriezellen sowie die nötige Technik untergebracht sind. Zwar sollten die einzelnen Zellen theoretisch alle gleich viel Energie speichern können. In der Praxis sieht das jedoch anders aus.
Herstellungsbedingt variieren ihre Kapazitäten. Das ist problematisch, da die Zellen in Reihe geschaltet sind. Die gesamte Batterie ist daher nur so stark wie die schwächste Zelle. Ist diese leer, nützt auch die restliche Energie in den anderen Batteriezellen nichts mehr – das Auto muss Strom tanken. Die Hersteller sortieren daher vor und bauen jeweils Zellen ähnlicher Kapazität in eine Batterie. Da dabei jedoch auch einige Zellen aussortiert werden, treibt dies die Preise der Batterien in die Höhe. Ein weiteres Manko: Ist eine Zelle defekt, bleibt das Fahrzeug liegen. Dann heißt es, den kompletten Stromspeicher auszutauschen.
Unabhängige Batteriezellen kommunizieren miteinander
Forscher am Fraunhofer-Institut für Produktionstechnik und Automatisierung IPA in Stuttgart haben nun eine Alternative geschaffen. „Unser modulares Batteriesystem löst diese Probleme“, sagt Dr. Kai Pfeiffer, Gruppenleiter am IPA. Der Trick: Jede Batteriezelle verfügt über einen eigenen integrierten Mikrocontroller, der relevante physikalische Parameter wie Temperatur und Ladezustand der Zelle erfasst. Jede Zelle kennt also ihren Zustand. Über die bereits vorhandene Hochstrom-Verkabelung zwischen den Batteriezellen, durch die gespeicherte Energie zu den Verbrauchern geleitet wird, reden die Zellen miteinander. Man spricht dabei von Powerline-Kommunikation. Oder sie kommunizieren mit anderen Geräten, etwa dem Bordcomputer, der aus den Daten der Zellen errechnet, wie viel Restenergie die gesamte Batterie noch aufweist.
Höhere Reichweite
Ist eine Zelle leer, während die anderen noch Energie gespeichert haben, muss das Auto nicht wie bisher stehenbleiben. Vielmehr klinkt sich die leere Batteriezelle einfach aus dem Verbund aus, sie leitet den Strom an sich vorbei. Die anderen liefern weiterhin Energie. „Je nach Zellqualität können wir die Reichweite auf diese Weise um mindestens vier Prozent steigern“, erläutert Pfeiffer. „Im Laufe der Zeit verstärkt sich dieser Effekt: Schaltet man bei einer älteren Batterie die jeweils leeren Zellen aus, ist es denkbar, dass man durchaus zehn Prozent mehr Reichweite erzielen kann.“
Da sich eine Zelle mit geringerer Kapazität kaum auf die gesamte Reichweite des Autos auswirkt, brauchen die Hersteller diese nicht mehr vorzusortieren. Dies dürfte die Kosten deutlich senken. Zudem passen sich die Kapazitäten der Zellen im Laufe der Zeit aneinander an. Denn die Varianten, die weniger Energie speichern können, werden früher ausgeschaltet. Die ergiebigen Zellen laufen dementsprechend länger und altern somit schneller: Ihre Kapazität sinkt. Und sollte eine Batteriezelle einmal ausfallen, kann man sich den Weg in die Werkstatt sparen. Da das Auto über mehr als hundert Zellen verfügt, kommt es auf eine einzelne Zelle nicht an. Und entscheidet der Fahrer sich doch für eine Reparatur, genügt es, anstelle der kompletten Batterie lediglich die einzelne Zelle auszutauschen.
Einen Prototyp der Batteriezelle haben die Forscher bereits entwickelt. Nun geht es daran, die Elektronik in den Zellen zu miniaturisieren. „Wir wollen es schaffen, dass sie weniger als einen Euro kostet“, so Pfeiffer. Teile der Entwicklung bearbeiten die Forscher im EU-Projekt "3Ccar" weiter.
---
Bild: Intelligente Batteriezelle des Fraunhofer IPA: Ein Mikrocontroller erfasst physikalische Parameter wie Temperatur und Ladezustand. Ist eine Zelle leer, klinkt sie sich automatisch aus.