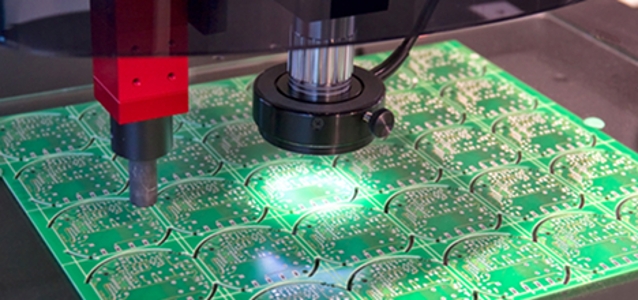
© alterfalter dreamstime.com
Leiterplatten |
Wenn die Fertigung Probleme macht
Viele Medizintechnik-Produkte enthalten eine hochwertige Elektronik, die Stückzahlen sind allerdings häufig klein und auch die verwendeten Bauteile sind oft speziell und untypisch. Das macht die Elektronikfertigung teuer. Das muss nicht sein, sagt der Elektronikfertiger Ihlemann und verweist auf seine Lean-Strategie.
Je spezieller die Baugruppen, umso häufiger müssen nicht normgerechte, atypische Bauteilgeometrien verarbeitet und häufig per Hand bestückt werden, was zu Qualitätsproblemen und teurer Nacharbeit führen kann. Solche Bauteile, die nicht dem Normstandard entsprechen, gibt es viele. Dazu gehören u. a. Stecker, Übertrager, Relais, Spulen oder Abschirmbleche. Sie werden häufig spezifisch und nur in kleinen Mengen produziert, sodass eine maschinengerechte Verpackung für den Hersteller nicht wirtschaftlich ist. Ohne diese maschinengerechte Zuführung in die Bestückungsautomaten bleibt nur die Handbestückung.
Die manuelle Verarbeitung dauert allerdings mehr als doppelt so lange und verzögert den Fertigungsablauf. Kommt es qualitätsbedingt zu Nacharbeiten, steigen die Kosten und die Fertigstellung des Produktes verspätet sich nochmals. Hier setzt die Ihlemann AG an.
Umstellung auf eine flexible Fertigung
„Wir haben die Krise 2009 dafür genutzt, um unsere Produktionsweise komplett zu verändern“, so Bernd Richter, Vorstand bei der Ihlemann AG. Der EMS-Dienstleister setzt seitdem auf Lean-Management-Prinzipien. Im neuen Fertigungsablauf erfolgen jetzt alle Tätigkeiten für jedes einzelne Board direkt nacheinander in einem verknüpften Prozess.
Dafür durchläuft auch ein komplexes Board in einer Fertigungszelle (U-Zelle) alle für den Produktionsprozess benötigten Arbeitsschritte direkt nacheinander. Das Board wird bestückt, getestet und noch in der Fertigungszelle auf Fehler geprüft und anschließend zur Auslieferung bereitgestellt. Grundlagen dieses Fluss-Prinzips sind tägliche Verbesserungsroutinen durch die Mitarbeiter in der Fertigung und eine kontinuierliche Unterstützung durch Coaching-Routinen. Die Veränderungen der Neuorganisation führten anfangs zu einer Vielzahl von Hindernissen.
Aus Sicht der Ihlemann AG macht besonders die Fähigkeit zur Überwindung solcher Hindernisse das Wesen der neuen Organisation aus. Durch einen tagtäglichen Verbesserungszyklus werden Veränderungen systematisch und mit festen organisatorischen Routinen bewirkt (Verbesserungs-Kata). Diese Fähigkeit, tagtäglich kleine Verbesserungsschritte zu erreichen und die Fertigung schneller und effizienter zu machen, wendet der Dienstleister auch bei der Verarbeitung „schwieriger“ Bauteile an oder um die Elektronikfertigung effizienter zu machen.
Hilfen für atypische Bauteile
Ein neues Medizinprodukt sollte mit einem Stecker mit 220 Pins automatisch bestückt werden. Das war die Zielvorgabe für den Verbesserungsprozess. Weil der Bauteilhersteller keine Standard-Verpackungsform für die maschinelle Verarbeitung bereitstellte, suchten die Mitarbeiter der SMD-Fertigungszelle nach einer eigenen maschinengerechten Zuführung.
Hier gab es bereits zahlreiche Erfahrungen mit der Entwicklung von Hilfsmitteln und Vorrichtungen, um Arbeitsprozesse einfacher und effizienter zu machen. Der Verbesserungsprozess durch die Mitarbeiter der Fertigungszelle startete mit einer ersten Idee, die geprüft und wieder verworfen wurde. Es folgte eine neue Idee, die bereits besser passte. Sie wurde wieder überprüft, verbessert, nochmals überprüft und über drei Monate in vielen kleinen Verbesserungszyklen soweit entwickelt, dass sie einsetzbar war.
Die Mitarbeiter hatten für den Stecker eine maschinengerechte Zuführung gefunden und die manuelle Bestückung konnte entfallen. Mussten anfangs 34 % der Stecker nachbearbeitet werden, verringerte sich die Quote durch das Hilfsmittel auf 0,5 %. Damit konnten die Kosten gesenkt, die Verarbeitungszeit des Steckers verkürzt und die Durchlaufzeit verringert werden.
Für die technische Umsetzung solcher Hilfsmittel verfügt der EMS-Dienstleister über einen eigenen Vorrichtungsbau. Die Vorgaben zur Umsetzung stammen von den Mitarbeitern, die den Verbesserungsprozess vorantreiben. Beim Bau solcher Zuführungen und anderer Hilfsmittel in der Fertigung verfügt der EMS-Dienstleister inzwischen über mehrjährige Erfahrungen.
Wenn die Fertigung Fehler meldet
Andere Probleme mit der Elektronikfertigung betreffen häufig die Abkündigung von Bauteilen oder die Nichteinhaltung von Designvorgaben:
© Ihlemann
Einhaltung von Designregeln
Zu den typischen Fertigungsproblemen gehören mangelhafte Lötstellen von Steckerleisten. Die Anschlüsse von solchen bedrahteten elektronischen Bauelementen werden per Durchsteckmontage (THT, through-hole technology) in die Leiterkarte gesteckt und anschließend durch Löten mit der Leiterbahn verbunden. Einer der typischen Fehlerursachen ist hier, dass beim Design der Leiterkarte die Kontaktlöcher für die Drahtanschlüsse falsch dimensioniert werden. So hatte es beispielsweise wiederholt Fehler gegeben, weil die Kontaktlöcher nur 0,1 mm größer waren als die Drahtanschlüsse. Das führte zu einer erhöhten Fehlerrate, weil beim Löten die Anschlüsse nicht zuverlässig kontaktiert wurden (mangelhafter Lötdurchstieg). Beim nächsten Re-Design wurden die Löcher deshalb auf 0,4 mm des Drahtdurchmessers vergrößert. Dadurch konnten Nachbearbeitungen vermieden und die Auslieferung beschleunigt werden.
Standards und Designrichtlinien
Probleme in der Elektronikfertigung werden vermieden, wenn in der Entwicklung und beim Design nationale und internationale Standards, die Vorgaben der Bauteilhersteller sowie spezifische Vorgaben der jeweiligen Fertigungsmaschinen genau eingehalten werden.
Softwaregestützte Design-Evaluierung
Bei der Design-Evaluierung wird die Bestückung digital simuliert und die Regelkataloge automatisiert angewandt. Mithilfe der Kataloge kann Ihlemann jetzt vor dem Beginn der Fertigung zuverlässig prüfen, ob die Bauteile auf die Leiterplatte passen, ob die Pad-Auswahl stimmt oder ob die Vorgaben der Bauteilhersteller eingehalten wurden. Die Ihlemann AG bietet diesen Prozess auch als Dienstleistung an.
Mit der digitalen Design-Evaluierung lassen sich bereits in der Entwicklungsphase eines neuen Boards nahezu alle layout- und designbedingten Fehler oder Probleme feststellen. Damit werden zeitaufwendige Korrekturschleifen und zusätzliche Prototypenfertigungen eingespart und das neue Board kann fertigungssicher in die Serie überführt werden.
Zu den Ergebnissen der Design-Evaluierung gehören auch Vorschläge für ein Re-Design, um beispielsweise eine Leiterbahn umzulegen, eine Durchkontaktierung neu zu platzieren oder die Abstände von SMD- und THT-Bauelementen zu optimieren.
- Ist der äußere Rand auf der Leiterplatte zu klein, kann sie in der Fertigungslinie nicht mehr richtig transportiert werden oder ein zusätzlicher Nutzen muss definiert werden.
- Fallen wegen Platzproblemen die Passermarken weg, funktioniert bei der automatisierten Bestückung die genaue Lageverifizierung der Leiterplatten nicht mehr und eine exakte Bestückung ist nicht mehr möglich.
